Warehouses are the nerve centers of modern supply chains. Efficiency, safety, and error free operations are paramount—but many still operate with outdated paper-based systems and siloed computer applications. These outdated workflows cause delays, mistakes, and safety gaps, hindering productivity and increasing operational risk.
With the emergence of easy, mobile connected worker apps designed for the frontline, digital transformation is no longer reserved for back-office functions. Today, intuitive digital tools can directly support frontline workers in areas like training, equipment maintenance, safety compliance, and even customer service to empower workers with visual guidance, embedded training, automated inspections, and AI‑powered assistance. Logistics and warehouse teams can use these tools to boost efficiency, reduce risk, and improve performance across core operational areas.
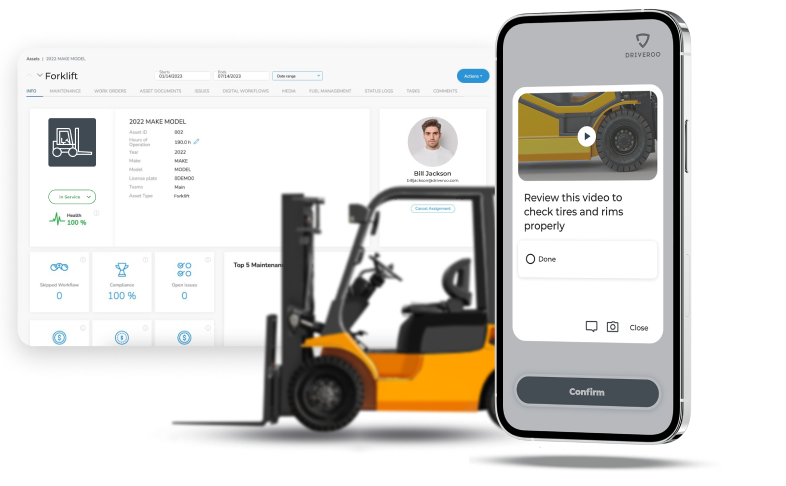
The Hidden Costs of Paper-Based Systems
Logistics and warehousing operations that rely on paper are absorbing unnecessary cost and inefficiencies, and increasing safety risks. Paper-based workflows in warehouses are error prone and often cause delays due to lost information. Inspections are slow, training is inconsistent, and maintenance issues go unnoticed, leading to unplanned equipment downtime. Critical safety steps are often missed, and data entry is unreliable. Digital tools streamline these processes, improving accuracy, visibility, and overall operational efficiency in several ways.
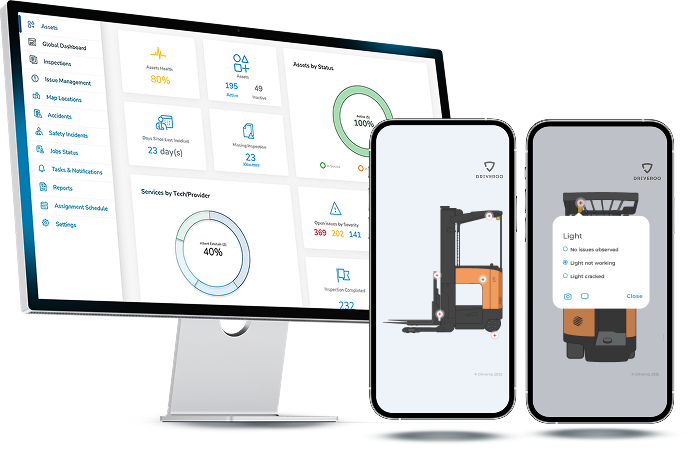
Onboarding and Training
High turnover rates and labor shortages make rapid onboarding a logistics business imperative. Traditional training methods—manual SOPs, job shadowing, and outdated paper manual often fall short in consistency and effectiveness. Digital solutions can deliver on the spot visual work instructions that walk new hires through tasks step-by-step using images or videos. Worker skills can be improved by enabling mobile-based training that workers can access on the job, at their own pace and convenience. Training progress and competencies can be tracked automatically, allowing supervisors to identify who is ready for more responsibility or who needs additional support.
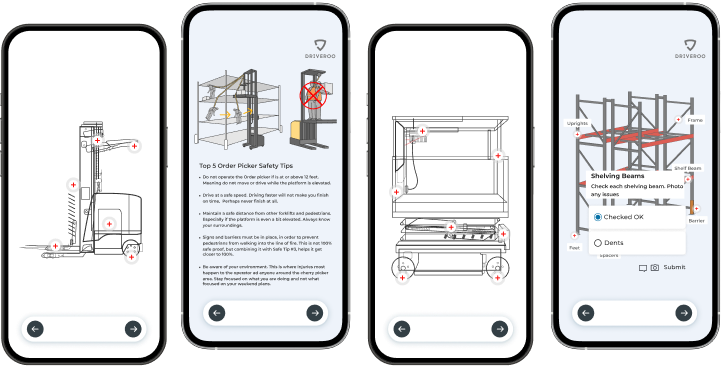
Standardizing and Streamlining Work
When relying on paper SOPs, driving for standardization in frontline processes is a challenge. Proper SOPs are rarely referenced and paper checklists are ineffective in ensuring that work processes are accurately followed. Digital tools offering Smart Inspections and Work Instructions replace traditional textual checklists with images that show exactly what needs to be inspected and how. Micro-training can be embedded directly in the workflows for easy access by workers when needed. Work processes can be documented for verification by images and video and completions can be tracked online, delivering managers instant visibility to progress.
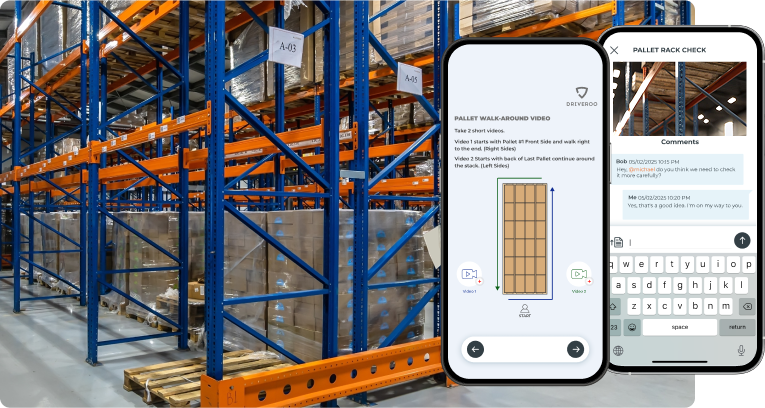
Equipment Maintenance and Reliability
Unplanned equipment downtime is costly. Reactive maintenance and undocumented repair histories can extend downtime and increase equipment operating costs. Adopting digital frontline solutions for equipment maintenance can facilitate scheduled preventive maintenance (PM) tasks with automated reminders and digital checklists. Equipment inspections with images and video enable maintenance teams to be more effective at responding quickly to equipment issues and ensuring first time fix. Repair work can be more easily assigned and completed when mobile work orders are tied to parts and warranty management systems.
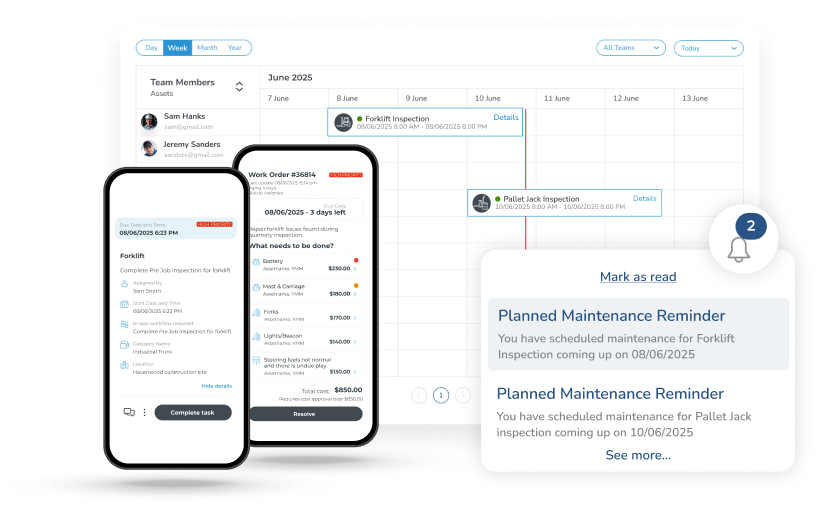
Safety and Compliance
Safety in a warehouse isn’t just about avoiding injuries—it’s also about ensuring compliance with regulations and reducing liability. However, when safety checks are done on paper or inconsistently, it’s easy for issues to go unnoticed. Digital tools can simplify safety checks, strengthen safety culture and ensure compliance with requirements such as OSHA and SQF regulations. Safety checks are facilitated with easy, visual guidance and data is automatically gathered for compliance reports and analysis.
Alerts and notifications can be sent when required checks and safety processes are delayed or skipped. Digital incident and hazard reporting makes it easier for frontline workers to engage in improving safety, and instant access to reported incidents speeds up response leading to safer working environments.
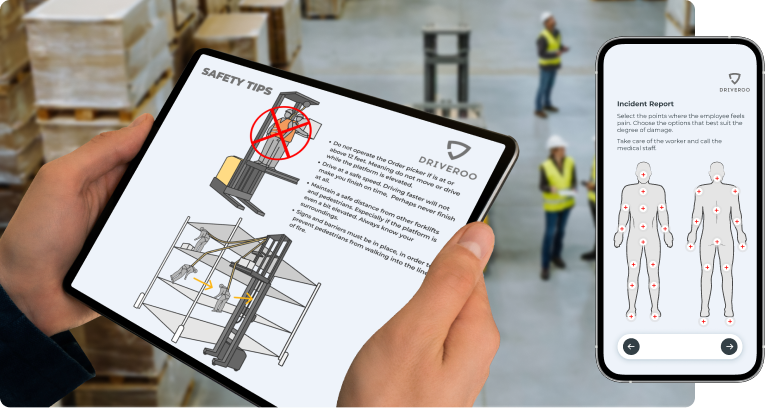
Customer Experience and Claims
Risk Management
Lost inventory, damaged goods, or worker errors can result in customer service issues and claims. Ensuring that the right goods are loaded and delivered to customers is one attribute of digital frontline tools, but the ability to quickly and clearly prove what was actually done can also save significant time and cost. Digital tools can easily document tasks with time-stamped entries and visual evidence (photos/videos) to support defensible claims resolution.
They also simplify maintaining digital audit trails for inspections, maintenance, and handling procedures. In some cases, the output from digital tools can also be used to provide customers with documentation useful for processing their shipments. When warehouse operations are transparent and well-documented, customer service teams are better equipped to respond quickly and accurately to inquiries or complaints.
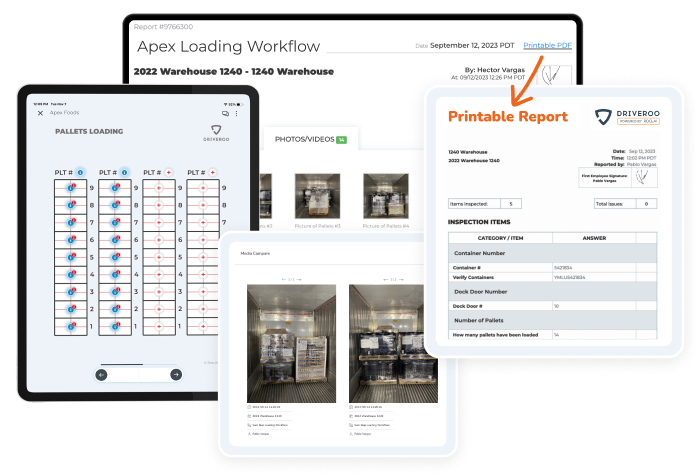
Getting Started With Digitalized
Frontline Logistics
Companies adopting digital platforms like Driveroo, powered by ROO.AI, report faster onboarding, fewer errors, safer operations, and lower costs. Getting started is easy and digital workflows can be operational within a couple of weeks without the need to involve company IT resources. These are some of the common best practices for getting started:
- Launch the platform for a specific team or warehouse.
- Digitize core workflows: inspections, maintenance, safety checks and onboarding.
- Customize visuals & logic to match your equipment and workflows.
- Track early KPIs, including task cycle time, compliance rate and downtime.
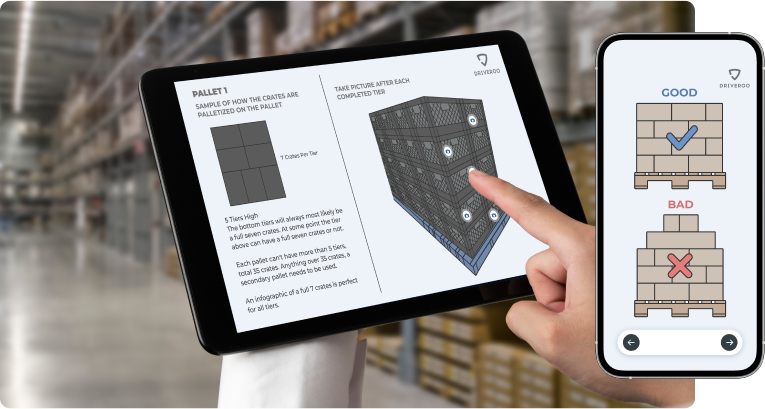
Building a Safer, Smarter Warehouse
Digital transformation in warehouse operations doesn’t have to be complex or expensive. Simple mobile tools like Driveroo, using visual workflows and automated reporting, can have a major impact on worker productivity, operational efficiency, and safety.
Whether you're onboarding a new team, managing a busy maintenance schedule, or striving to meet higher compliance and service standards, digital tools offer practical, scalable solutions that connect your frontline workforce to real-time information and support.
By modernizing these core processes, warehouses can not only boost output and safety but also build more resilient, responsive, and future-ready operations.
Driveroo intuitive visual interface, on the spot guidance, and automated data capture empower frontline workers with instant support while equipping businesses with actionable insights for smarter, data-driven decision-making.